Bioabfallbehandlung
Mechanische Aufbereitung und Methanisierung
Die mechanische Aufbereitung und Methanisierung sind der erste Anlagenteil der Mechanisch-Biologischen Bioabfallbehandlung (MB2A), die ihrerseits Bestandteil des Biomasse-Kompetenzzentrums ist. Der Bioabfall wird von den Sammelfahrzeugen aus Stadt und Landkreis Kaiserslautern sowie den Containerfahrzeugen aus den Umladestationen der GML-Gesellschafterkommunen bei uns angeliefert, wo er im Aufgabetrichter der VM-Presse landet.
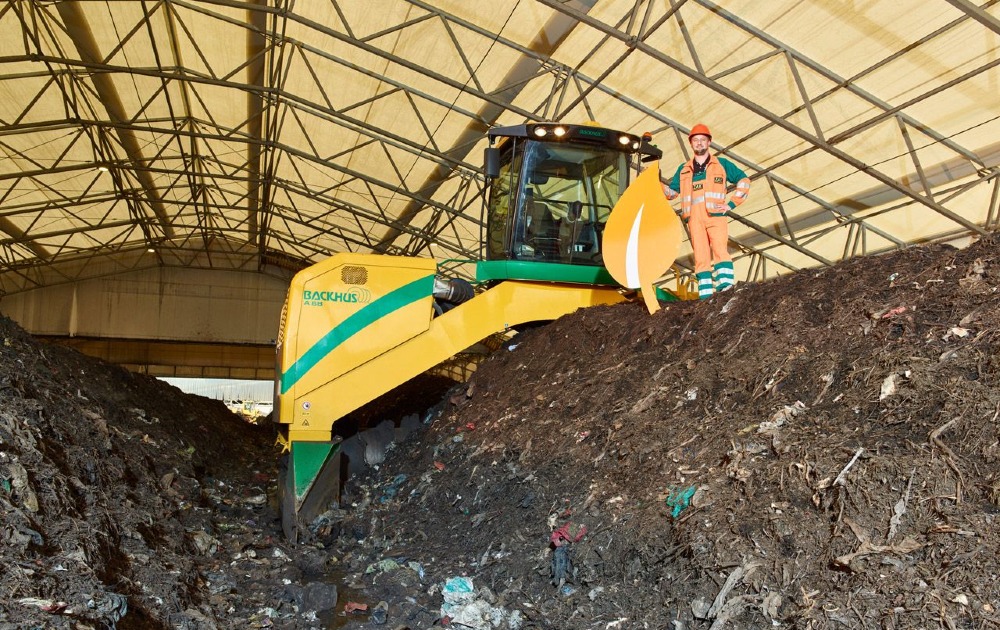
Brückenumsetzer
In der VM-Presse erfolgt die Aufteilung des Bioabfalls in eine Grob- und eine Feinfraktion. Herzstück der VM-Presse sind Trommelsiebe, in denen der Bioabfall mit einem Hydraulikdruck von etwa 50 bar gepresst wird. Die Feinfraktion wird in der Methanisierung nach dem Dranco-Verfahren anaerob behandelt und dadurch Biogas gewonnen, das zur Strom- und Wärmeerzeugung genutzt wird. Die Trockenfraktion aus der VM-Presse wird zusammen mit dem Gärrest aus der Methanisierung in einen Mischer geführt und intensiv aerobisiert sowie homogenisiert.
Aerobe Abbauprozesse
Der durchmischte Bioabfall fällt aus dem Mischer in eine Verladestation und gelangt von dort in Rotteboxen. In diesen Boxen erhitzt sich das Material durch biologische Abbauprozesse, so dass es bei einer Temperatur von über 60 Grad in einem Zeitraum von mindestens sechs Tagen hygienisiert wird. Danach wird das Material per Radlader zu Mieten aufgesetzt und mehrfach mit einem Brückenumsetzer gewendet, so dass der Rotteprozess startet.
Hochwertiger Biokompost
Im abschließenden Schritt wird das Material in mehreren Stufen von störenden Fremdstoffen befreit. Es findet eine Grob- und eine Feinsiebung statt, Eisenmetalle werden abgetrennt, mittels Röntgentechnik werden Glaspartikel und mit Nahinfrarotspektroskopie Kunststoffpartikel erkannt und mit Druckluft entfernt, so dass ein hochwertiger Biokompost entsteht, der in der Landwirtschaft als Düngemittel, Humusbildner und Wasserspeicher genutzt wird.
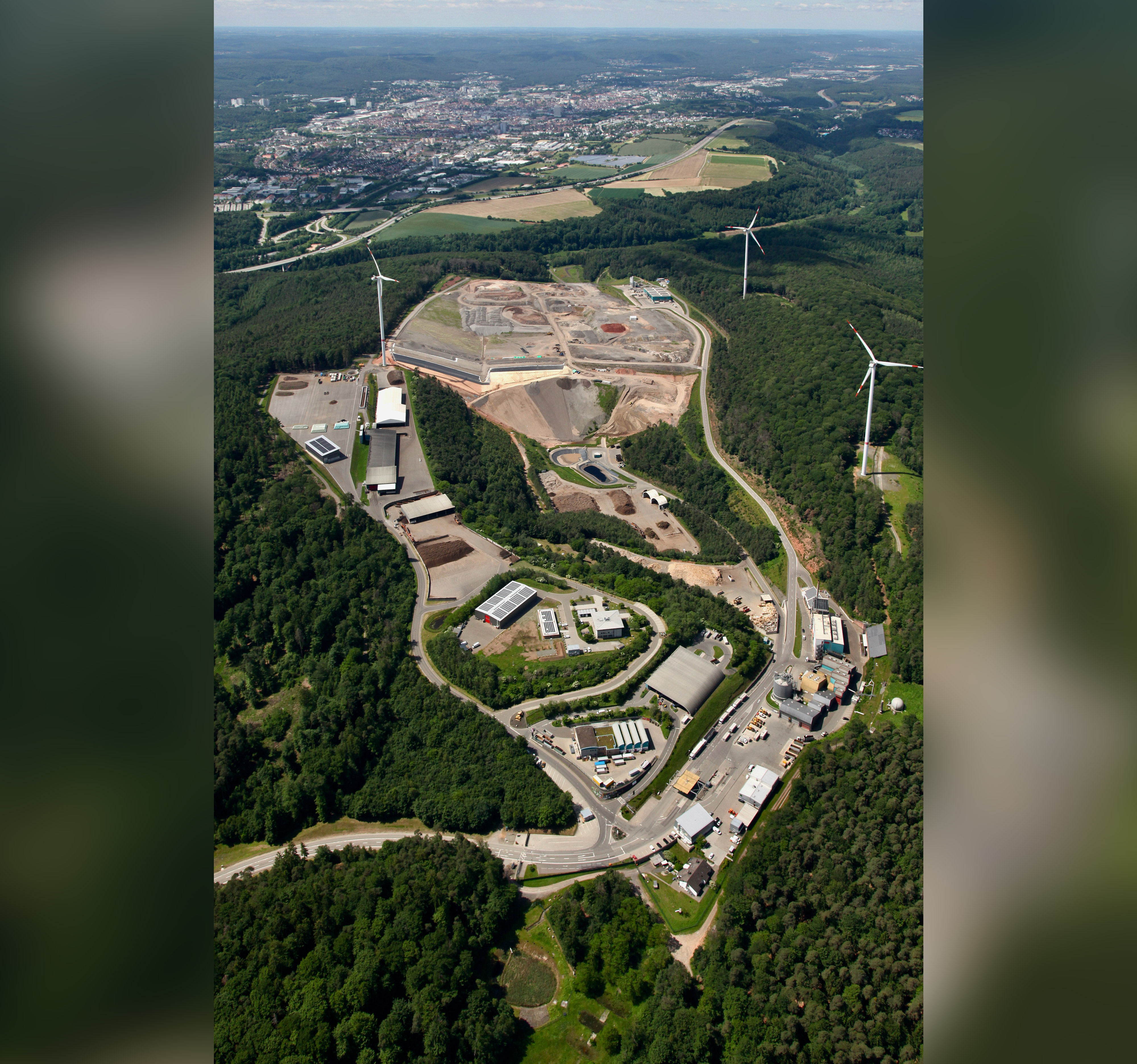